Introduction
Hardwood timbers are the backbone of many woodworking projects, known for their strength, beauty, and durability. But before they become the polished pieces we use in furniture, they start as rough sawn timber. In this blog post, we'll explore the journey of hardwood timbers from rough sawn to machined perfection, the average widths of various hardwoods, and the importance of jointing for creating wider panels.
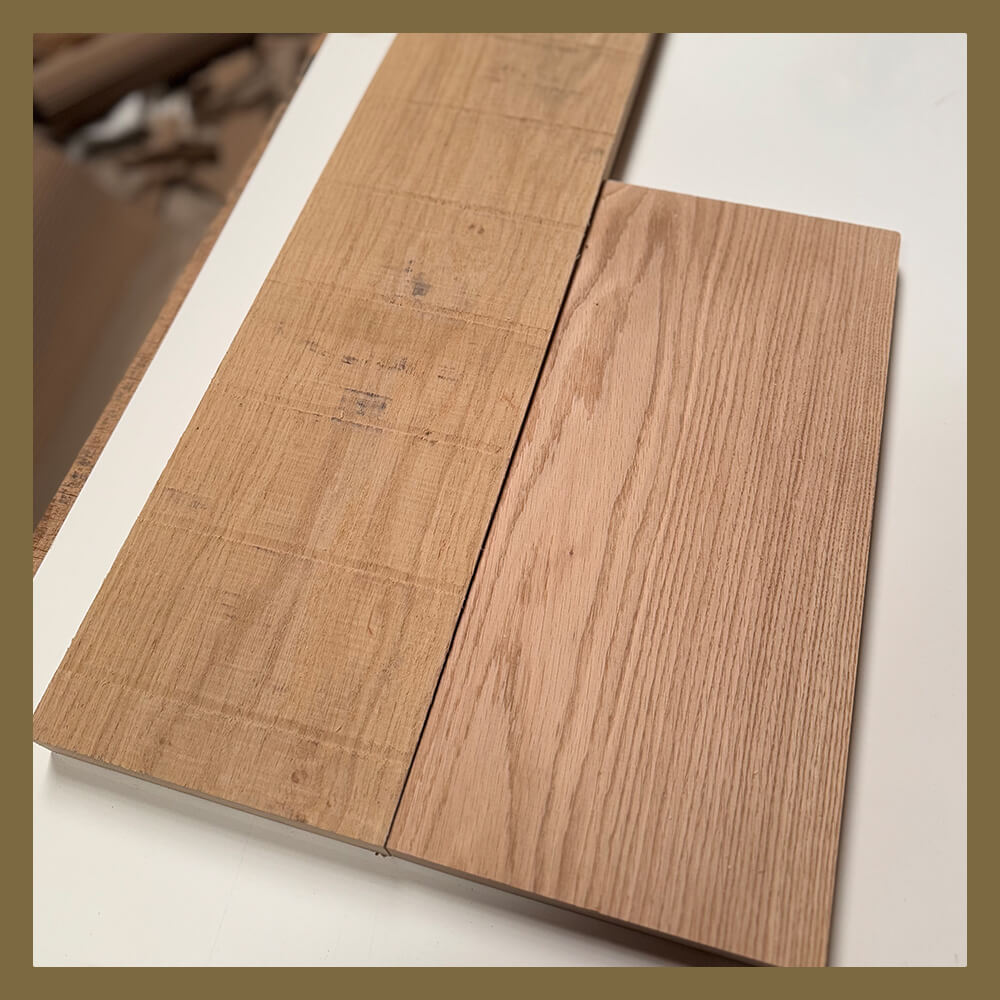
1. Rough Sawn Lumber
What is Rough Sawn Lumber? Rough sawn timber is wood that has been cut from logs into planks or boards but has not been planed or sanded to a smooth finish. It retains its rough surface and is usually sold in various thicknesses and widths, depending on the type of wood and the sawmill's cutting practices.
Advantages of Rough Sawn Lumber
Cost-Effective: Rough sawn lumber is generally more affordable than machined wood since it requires less processing.
Customization: Woodworkers can customize the dimensions to suit their specific project needs.
Character: The rough texture and natural imperfections add character to the wood, which can be desirable for certain projects.
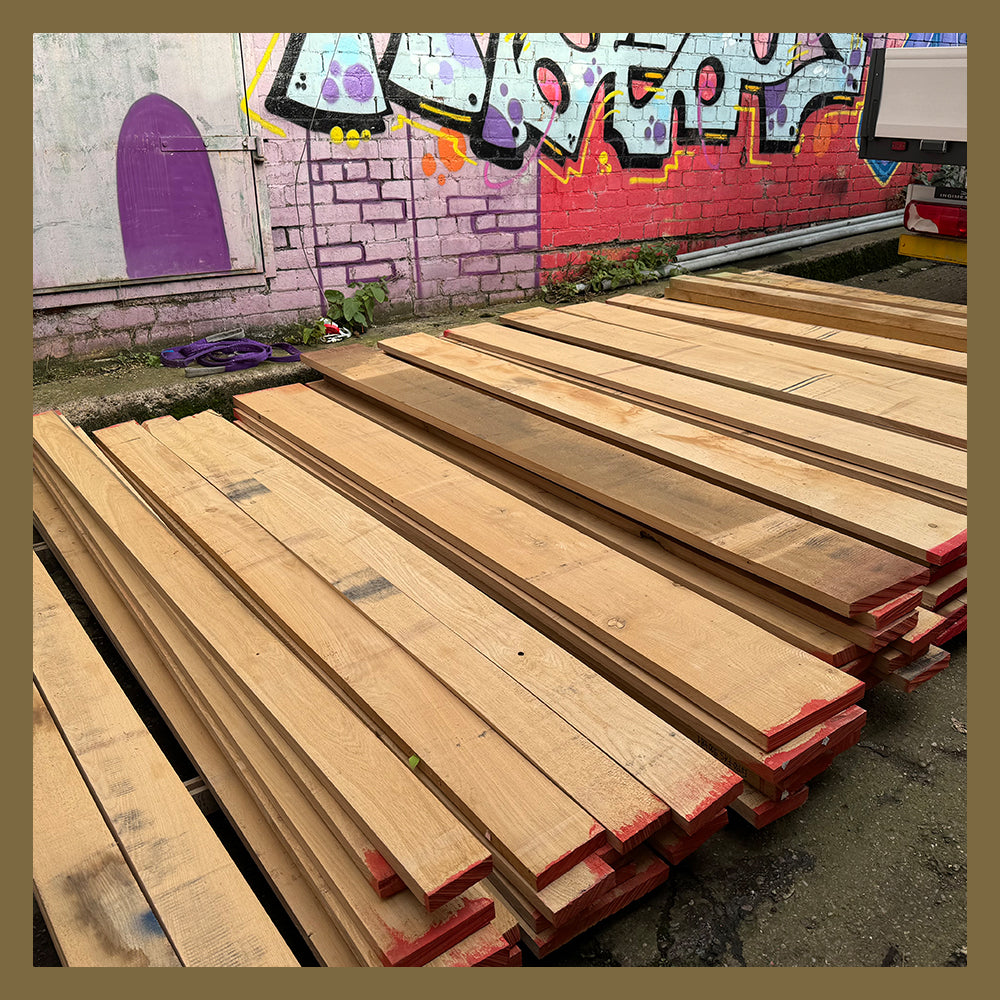
2. Machining Hardwood Timbers
Planing and Thicknessing The first step in machining rough sawn lumber is planing and thicknessing. This process involves passing the wood through a planer to remove the rough surface and achieve a consistent thickness. The result is a smooth, flat board ready for further processing.
Jointing and Edge Machining After planing, the edges of the boards are jointed to create straight, square edges. This step is crucial for ensuring that the boards fit together seamlessly when glued or assembled. Jointing also removes any warping or irregularities from the edges.
Sanding and Finishing The final machining steps involve sanding the wood to achieve a smooth surface and applying any desired finishes, such as staining, sealing, or varnishing. These steps enhance the wood's appearance and protect it from wear and environmental factors.
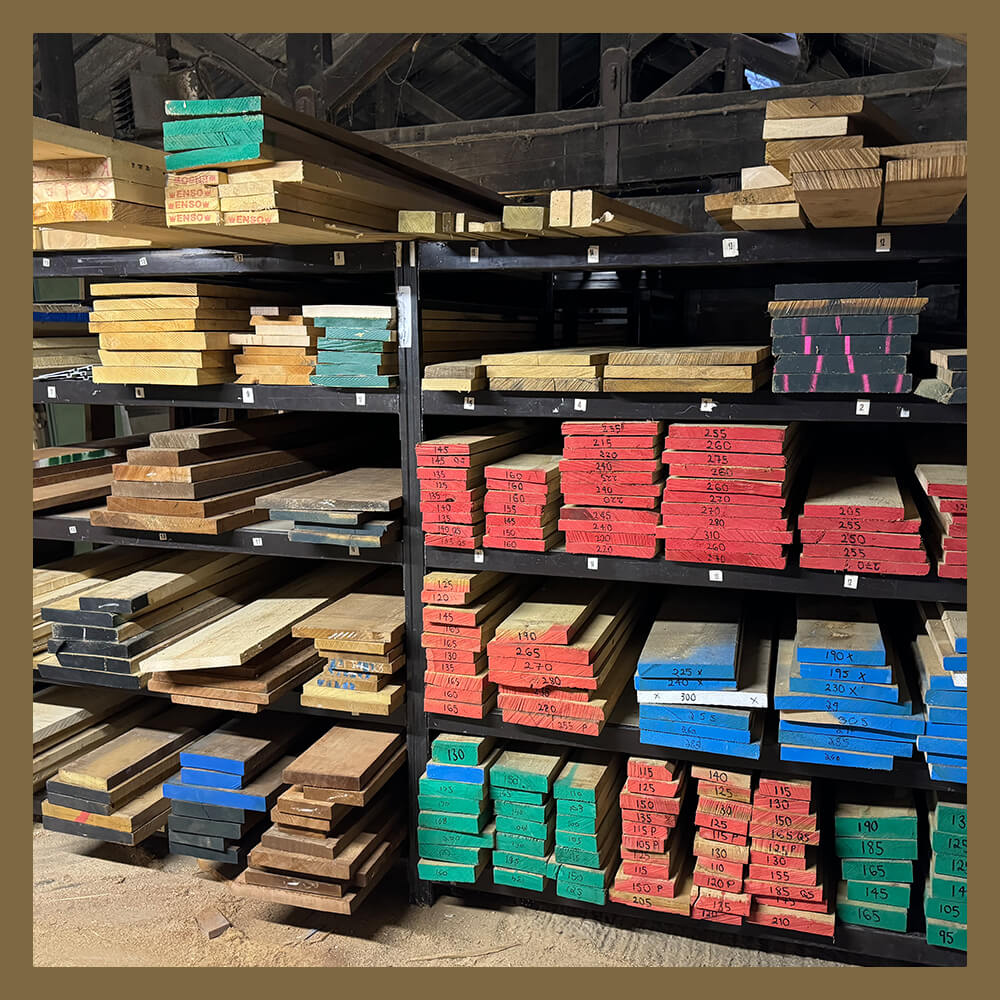
3. Average Widths of Hardwood Timbers
The average widths of hardwood timbers can vary based on the species and the source. Here are some common hardwoods and their typical rough sawn widths:
European Oak: 6 to 9inches (15 to 22.5cm)
Iroko: 4 to 12 inches+ (10 to 30cm+)
Sapele: 4 to 12 inches+ (10 to 30cm+)
Walnut: 4 to 10 inches (10 to 25 cm)
Maple: 6 to 10 inches (15 to 25 cm)
Beech: 6 to 10 inches (15 to 25 cm)
Ash: 6 to 10 inches (15 to 25 cm)
These widths are approximate and can vary based on the specific log and sawmill practices.
Please get in touch for wider boards, sizes stated are averages which we can get regularly. Wider stock in oak and walnut tends to have a high selling price due to purchasing WIDE only packs.
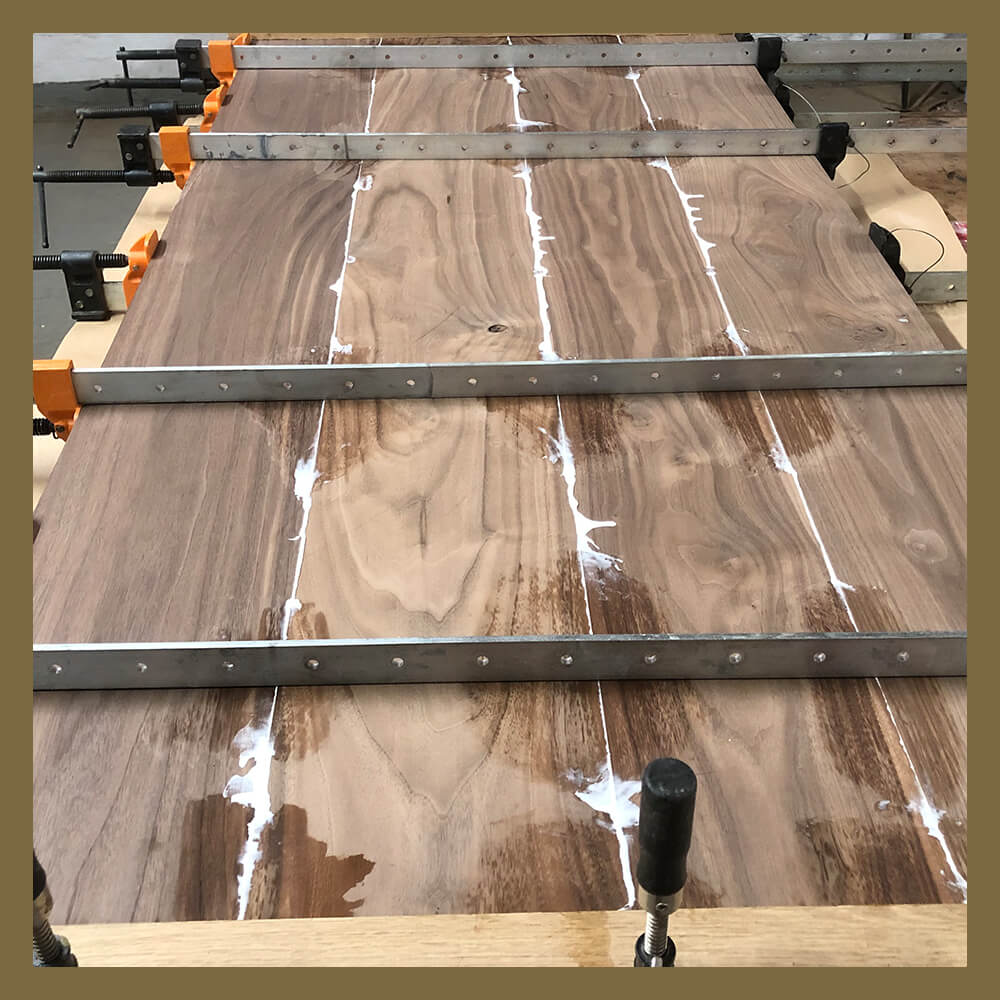
4. The Importance of Jointing for Wider Panels
Why Joint Timber? Most timber for furniture is jointed to create wider panels because the natural width of individual boards is often insufficient for large surfaces like table tops or cabinet sides. Jointing allows woodworkers to join multiple boards edge-to-edge, creating a seamless, wider panel. If you do want to work with wide pieces and tree slabs the acclimatisation process is your best friend!
Benefits of Jointing
Stability: Jointing helps to reduce the natural tendency of wood to warp or cup. By alternating the grain direction of adjacent boards, the panel becomes more stable.
Aesthetics: Jointing allows woodworkers to match grain patterns and create visually appealing panels with consistent appearance.
Customization: Wider panels can be created to match specific project requirements, offering greater flexibility in design.
Conclusion: The journey of hardwood timbers from rough sawn to machined perfection involves several steps, each contributing to the final product's quality and usability. Understanding the average widths of hardwoods and the importance of jointing for wider panels is essential for any woodworker looking to create beautiful and durable furniture. By mastering these processes, you'll be well on your way to crafting stunning pieces that will stand the test of time.